 |
 |
|
|
 |
 |
 |
Materials: At Rainforest Designs Ltd., we hand craft a wide variety of Nimbus(R) ocean touring kayaks, from our smallest single, the Cygnet, to our largest double, the Skana. Nimbus(R) kayaks are designed for functionality and manoeuvrability, while maintaining graceful lines, making them a pleasure to paddle and a treasure to own. |
 |
素材:レインフォレスト・デザイン社では、ニンバスの多種に渡るシーカヤックの一番小さなシングル艇であるシグネットから最大を誇るダブル艇のスカーナまで、丁寧に手作業で製作しています。ニンバスカヤックは、優雅な形を保ちながらも機能を求めた機動性のあるデザインを取り入れているので、パドリングの楽しさを得ると同時にあなたの宝物となるはずです。 |
 |
Resin: We use a vinyl ester based resin that is tougher and absorbs less moisture than cheaper polyester resin. The vinyl ester we use for all our composite kayaks has a molecular backbone very similar to epoxy resin, resulting in a stronger, longer lasting boat. |
 |
樹脂:安いポリエステル樹脂より、粘りがあり湿気を吸収しにくいと言われているビニールエステルが主成分の樹脂を使用しています。ニンバスカヤックの全てに使用しているビニールエステルは、分子間に存在している要素がエポキシ樹脂と同等であり、結果として頑丈で長い寿命につながっています。 |
 |
Gelcoat: We use only more expensive NPG gelcoats, which are harder wearing, for our exterior finish on kayaks; so, as our boats get older, the finish looks better and lasts longer. |
 |
ゲルコート:ニンバスではカヤックの外側表面に高価なNPGゲルコートのみを使用しています。これは消耗を抑えるので、カヤックが古くなってくると、表面の見た目が良くなりさらに長持ちします。 |
 |
|
ページトップへ▲ |
 |
Cloth: We use woven or sewn materials wherever possible, resulting in a stronger, lighter kayak due to higher fibre content compared to one built with mat (CSM). We use a finely woven glass cloth against the gelcoat on all our boats. Our vacuum-bagging technique allows us to use this tightly woven fabric, which results in less material print-through than you would get using a heavy woven roving or coarsely woven material as the first layer. |
 |
ガラスクロス:可能である限り、編んであるもしくは縫い合わせてあるガラスクロスを使用しています。この結果、CSMのマットで作られたカヤックに比べて、繊維が密に詰まっている分、軽く頑丈なカヤックに仕上げられます。ゲルコートに対しては、編み目の細かいグラス材のガラスクロスを使用します。バキュームバッグ製法ではきつい編み目の布も使用できるので、結果として、厚みのある生地や目の粗い生地を基礎の層として使用しなければならない場合に比べて、少ない素材で形を形成することが可能です。 |
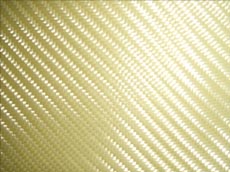 ケブラークロス | 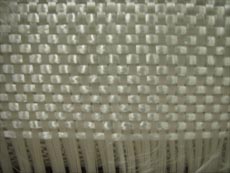 ガラスクロス |
|
 |
Reinforcement: We use a variety of materials for specific reinforcement of stress points in our kayaks. We include extra glass material in the bow and stern for abrasion resistance and Kevlar(R); to provide extra impact resistance. Additionally, all hulls and decks are reinforced with unidirectional glass to add extra strength and stiffness where needed. |
 |
強化材:カヤックに圧力のかかる特定の場所に多様な素材を補強材として使用しています。バウとスターンには、摩耗抵抗の為にグラス材を、そして衝撃抵抗を増強するためにケブラーを追加しています。さらに、ハルとデッキの必要な部分には、同方向に編み込んであるグラス材を追加し補強する事により、さらなる頑丈さと硬さを出しています。 |
Steve's design objective is to produce kayaks that best suit the comfort and needs of paddlers, while maintaining the beauty of line and high quality of construction for which Nimbus(R) has become well known. To do this, he carefully designs each kayak himself and tests it in the development stages. When he is satisfied with the design, a mould is built and carefully finished. Then each kayak is hand crafted using the best materials and methods available today. However, the work doesn't stop there. Steve constantly strives for ways to improve his kayaks and construction techniques. |
 |
スティーブのデザイン目的は、ニンバスの名が広く知れ渡るようになった理由である優美な形と、クオリティの高さを保ちながら、快適さを求めるパドラーのニーズに答えるカヤックを作り出す事です。この為に、スティーブ自身が全てのモデルをデザインし、発展させていく過程でテストを重ねています。彼自身がデザインに満足した後、モールド成形し入念に仕上げます。それぞれのカヤックは、現在入手可能な中での最高の素材と技術を使い手作業で製作されています。そして、仕事はそこで終了する訳でなく、カヤック本体や製造技術を改良させる為に、スティーブの奮闘は日夜続いています。 |
 |
|
ページトップへ▲ |
 |
Vacuum bagging technology is the best process presently available to produce composite kayak hulls and decks. It results in a more homogeneous, tougher laminate than that which results from a hand lay-up. These superior laminates are produced by compressing the fibreglass/Kevlar(R); by approximately seven pounds per square inch while laminating the hull or deck. This vacuum bagged laminate has a higher fibre content than a hand lay-up, which means that for equal weight, vacuum-bagged laminates are far stronger with more fibre and less resin (the weakest component in the laminate). The end result is stronger, better-built kayaks. The very nature of how vacuum-bagged laminates are made results in either very good laminates--or very bad ones, if things go wrong. |
 |
バキュームバッグ製法は、ハルとデッキを合体させる技術の中では現在最高の製造技術です。結果としてより均質的になり、手作業によるハンドレイアップ方式より遥かに頑丈なラミネート(薄板状)に仕上がります。この上質なラミネートは、ファイバーグラスとケブラーの圧着によって生産されています。ハルとデッキ部を例にとれば、1平方インチ(約6.45cm四方)に約7パウンド(約3.17kg)の圧力をかけてラミネート加工をしています。このバキュームバッグ製法は、手作業によるハンドレイアップ方式に比べて繊維が詰まった状態に仕上がる為、同じ重量で比較するとはるかに強度が高まります。ラミネート加工に使用されている構成成分の中で樹脂が一番弱い成分なので、最小限の樹脂しか残らないバキュームバッグ製法では、最終的な結果として強靭で良い仕上がりとなるのです。バキュームバッグ製法の結果はとても自然な形で現われます。とても良いラミネート加工に仕上がるか、何かの調子が悪くて最悪の仕上がりとなるかです。 |
 |
The other advantages of vacuum bagging are: the resin is fully-cured on the inside surface because the vacuum bag separates the surface from the air during the curing process (most fibreglass laminating resin is air-inhibited, which means that it never fully cures when left exposed to the air). The resulting glassy smooth inside surface of the kayak means gear, footwear and skin will not be exposed to the abrasion common in a kayak made by hand lay-up. The fully cured inside surface is also much easier to keep clean. Another plus for vacuum bagging is that the process is clean: resin is sealed under a nylon bag while the part is worked on, resulting in fewer volatile organic emissions (we wouldn't be building kayaks if we had to hand laminate them). |
 |
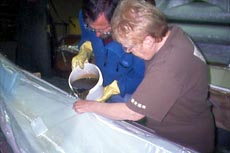 モールド中央に樹脂を流し込む | バキュームバッグ製法のさらなる利点としては、ビニールシートが空気を完全に遮断することにより、樹脂がカヤックの内面側でも完全に硬化する事です。ファイバーグラスをラミネート加工する際の樹脂は、空気によって硬化が妨げられやすく、外気にさらしたままでは完全に硬化せず乾燥処理されません。さらにカヤック内部の表面も硝子のように滑らかに仕上がるので、ハンドレイアップ方式にありがちな内面のざらつきが、道具やブーツ、さらに肌などに擦り傷を負うことを防ぎます。もう一つの利点は、その製法がクリーンであることです。樹脂がビニールシートの中に密封されているので、揮発性の有機物の放出を軽減する事ができます。(もし私達が従来の手作業によるハンドレイアップ方式で製造を続けていたとしたら、もうカヤックメーカーを辞めていたことでしょう。) |
 |
|
ページトップへ▲ |
 |
Quite simply, vacuum-bagging technology is superior--the only disadvantage is the extra cost. Additional equipment, materials and labour are required for this technique. We feel the benefit, in terms of value added to our kayaks as a result of this vacuum bagging procedure, far outweighs the drawback of the added cost. |
 |
簡単に言えば、バキュームバッグの技術は最も優れた製造方法です。しかし、この技術を使う為に新しい装置、新素材、そして人員配備をする必要があった為、たった一つの不利な点としてはコストがかさんでしまいました。しかし、バキュームバック製法により、ニンバスカヤックに付加価値が生じ、高価になってしまう欠点に勝る利益を提供出来ていると信じています。 |
 |
We spend more time finishing our kayaks than do other manufacturers. For example, we take great care joining the decks and hulls of our kayaks. This is one of the most important steps in the construction of a kayak. Our boats are seamed inside and out, with extra time spent getting outside seams on smoothly. We prepare the surface where the outside seam is installed to ensure a good bond; laminate a layer of fibreglass tape in place; fill the weave in the tape and sand it smooth, taking care to feather the edges; then retape the seam and apply gelcoat to it. (Few, if any, manufacturers perform all these steps.) |
 |
私達は、他のメーカーに比べて、作成の行程と仕上げに長い時間を費やしています。例えば、ハルとデッキの合体作業には、とても注意を払います。カヤックを組立てて行く上で、最も重要なステップだと考えているからです。ニンバスカヤックは、内側と外側の両方からシームが施されており、特に外側のシームは滑らかな仕上げになるようさらなる時間を費やします。外側のシームが確実に接着されるよう前もって表面の準備をし、ファイバーグラスのテープをラミネート加工する場所に配置させ、テープの編み目を樹脂で満たし、小さな突起などが残らないようヤスリをかけて表面を滑らかにします。そしてシームの上にさらにテープを貼りゲルコートで覆います。(もし全く同じ行程で作成している企業があるとしても、ほんの数社だけでしょう。)。 |
 |
We craft all of our kayaks using closed molding techniques. These methods are a considerable advance on the more common method of hand laminating. The primary process we use for our hulls and decks is called vacuum bagging but it is more accurately described as Squeegee Assisted Infusion (SAI). How it works in quite simple: all the materials are precut and placed in the mould with extra reinforcement where needed. A nylon bag is then sealed to the flange on the mould and the air evacuated from between the mould and the bag with a vacuum pump. This causes the atmosphere to compress the layers of fabric together with a about pressure of about 7 lbs per square inch. |
 |
ニンバスカヤックは、全てクローズドモールディング技術を採用して作成されています。この技術は、一般的な手で素材を張り合わせるハンドレイアップ方式よりも優れていると考えられます。ハルとデッキ部の製作には、第一のプロセスとして、バキュームバッグ製法を採用しています。正確な言葉で述べるとSqueegee Assisted Infusion (SAI)、(余分な注入物を絞り出す製法)と呼ばれる、とてもシンプルな製法です。最初に素材を必要な大きさに切り取り、補強部分の素材も併せて一緒にモールド(型)に位置させます。その上にビニールシートをかぶせ、モールドのフランジ(縁)を封印します。そしてバキュームポンプでモールドとシートの間の空気を吸い取ることにより、1インチ四方に3kgの圧力をかけて繊維の層を圧着させます。 |
 |
|
ページトップへ▲ |
 |
We then open the bag and introduce the resin in the middle of the mould, distribute it along the length of the mould, reseal the bag and reapply the vacuum. Then we use squeegees to help the vacuum pull the resin through the fabric that is not yet saturated. This process yields a better, more homogeneous and tougher laminate than hand laminating; up to 70% fibre content as compared to a hand laminate at 50% and, just as importantly, seals the resin under a nylon bag, greatly reducing the emission of VOCs and vastly improving the work environment. I am astounded that a lot of our competitors still fabricate their hulls and decks by hand laminating. |
 |
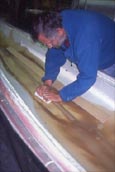 ゴムへらで樹脂を均一にのばす | そこで一度シートを開け、モールドの中央に樹脂を流し込みます。モールドの長さに沿って樹脂を広げた後、再度シートを封印し中の空気を吸引します。そこでゴムへらを使用し、繊維に染み込み切らなかった余分な樹脂を絞り出し、機械で吸引します。この方法は、素材を一体化させ、薄く、固く、無駄を省けるため、軽量化が図れます。ハンドレイアップ方式では繊維比率が50%にしかならない所、この方式では70%までに増大させることができるのです。また、樹脂をビニールで封印して作業を行う為、異臭の放出を軽減でき労働環境の向上につながっている事も大切な事実です。しかし、驚いたことに競合他社のカヤックメーカーは、未だに手作業をしている所が少なくありません。 |
 |
We use a slightly different process to make our FRP bulkheads, foam cored lids and cockpit coamings and hatch rims. This process is vacuum infusion in which we rely on the vacuum itself to distribute the resin without any manual assistance. It has taken us a couple of years to convert most of our moulds to this process which yields better parts. An added benefit is that our bulkheads are now translucent and make seeing what you have in the hatches easier. |
 |
FRPのバルクヘッド、ハッチカバー、コックピットコーミング、とハッチのリムについては、少し違った製法で作られています。これはバキューム注入製法と言って、全く人の手による作業を会せず、機械が樹脂をまんべんなく行き渡らせる製法です。この製法が確立されるまで、様々な型を改良することに数年かかりましたが、良い製品を作るには必要な時間でした。さらなる利点として、バルクヘッドが半透明となり、ハッチの中が見えやすくなったことも付け加えておきましょう。 |
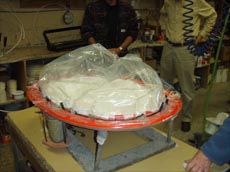 ハッチカバー製作(バキュームバック製法) | 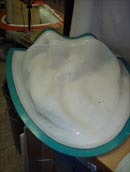 ハッチカバー製作 |
|
 |
|
ページトップへ▲ |
 |
The materials we use are somewhat different from those used by most of our competitors. We use only 100% vinyl ester resins in our hulls and decks as the slight extra expense is completely offset by the improved performance and longevity. |
 |
ニンバスカヤックに使われている素材は、他のカヤックメーカーが使用しているものと少々異なります。ニンバスでは、ハルとデッキの部分にはビニールエステル樹脂100%だけを使用しています。これを使用する事で少々コストはかさんでしまいますが、パフォーマンスの向上と長年維持可能という事実において、完全に埋め合わせされると考えます。 |
 |
We use a lot on non-crimped fabrics which offer technical advantages over woven fabrics in that the fibres can be optimally oriented and not weakened by weaving. Most of these fabrics have a polyester thread woven around the fibres which adds more impact resistance to our glass and kevlar laminates. We are the only kayak manufacturer to use this kind of hybrid fabric (glass/kevlar) as the outside layer of our Kevlar kayaks where we have glass fibers running transversely, while the kevlar fibres run longitudinally. The hulls on our glass kayaks have a glass/polyester inside layer which adds considerably to their impact strength and reduces the weight slightly. All our kayaks are selectively reinforced to add strength where needed. All our kayaks have kevlar reinforcement strips in the bow and stern. All our kayaks have FRP inside seams as well as outside seams. We spend extra time on our outside seams applying the glass tape after careful preparation and then filling and sanding it smooth before applying the finished colour. |
 |
技術上の利点から、ほとんどの繊維素材にはひだのついていないものを使用しています。これは編みのひだが残った繊維以上に素材の強度を出す事ができるからです。これらの繊維はポリエステルの糸で編み込まれているので、その結果、ラミネートされたグラスもしくはケブラー素材の衝撃に対しての抵抗力が高まります。カヤックメーカーの中で、このようなハイブリット繊維を外面部分に使用しているのはニンバスだけです。例えば、ケブラー製のカヤックでは、ケブラー繊維が縦軸に配置されたものにグラスファイバー繊維を横切るように編み込んであります。また、グラス製カヤックのハルには、グラスとポリエステルの混紡された繊維を内側の層に配置することにより、衝撃強度を高めた上に重量を軽くすることができました。ニンバスのカヤックは、全てのモデルで強度が必要な特定の部分にきちんと補強材を使用しています。例えば、バウとスターン(上陸等で一番擦りやすい部分)の強化にはケブラーの補強材を使用しています。また、本体接合部においては、内側と外側の両方にFRPのシーム剤を使用しています。外側のシーム部分には、念入りな下準備をした後にグラステープを貼るという手間もかけています。そして気泡を詰め物で塞いだり、ヤスリで研いだりした後に最終的な塗装を施します。 |
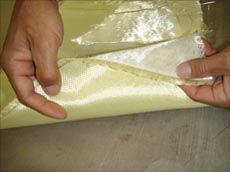 ニンバス社だけが取り扱うハイブリッド繊維 | 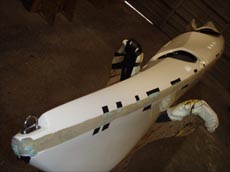 最終仕上げ |
|
 |
|
ページトップへ▲ |
 |
Our seams add significant strength to this joint between the hull and deck for minimal weight gain. |
 |
このシームの製法によって、ハルとデッキの接合箇所の強度を大幅に高め、軽量化につなげる事ができました。 |
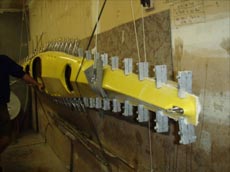 デッキとハルのカップリング(本体接合) | 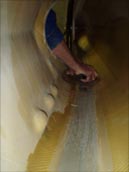 内側のシーム処理 |
|
 |
All our touring kayaks come with our "Creature Comfort Seat" as standard equipment. These seats are very comfortable and are easy to modify to suit those with particular preferences. The seat is comprised of a contoured foam seat base, which is covered by a mesh sleeve to which an adjustable backrest is attached. You can change the length of the seat base by sliding the mesh cover around the foam seat and repositioning the backrest. You can also adjust the tilt of the seat base by changing the foam wedge under the front of the seat. (This ability is especially important for those paddlers who are prone to having their legs fall asleep.) The width of the seat is adjustable by a set of hip pads which clip in place and have several settings. The contoured foam seat can also be modified for a custom fit by simply trimming away excess foam with a razor knife. As a alternative, add a Thermarest Sport SeatTM between the foam pad and the mesh cover with the valve sticking out the side. Deflate until comfortable. Please note: care should be exercised to not significantly change the kayak's stability while doing this. One final unique adjustment of our seat system is the ability to change the position of the entire seat fore or aft in the cockpit. This allows paddlers of different sizes the ability to balance the kayak for their particular weight distribution. |
 |
ニンバスカヤックの全モデルは、『人間に快適なシート』が標準装備として付いています。このシートはとても快適で、いろいろな好みや要望に合わせて簡単に各部を調整することができます。シートは発砲ウレタンフォームが土台となった形で構成され、筒状のメッシュ素材でカバーされたものにリクライニング機能のある背もたれが付いています。フォームシートを包んでいるメッシュカバーをずらし、背もたれの位置を調整することで、シートベースの長さを調整する事ができます。また、シートの前方の裏にあるくさび形をしたフォームを移動させることで、シートベースの傾きや太股周辺の高さを調節することができるので、足がしびれやすい人などには特に重要な機能です。シートの幅は、4段階に調節可能なヒップパッドが左右に標準装備され、いろいろなセッティングができ調整可能です。フォームシートの形もナイフで削ったりすることで、自分の望むフィット感に修正ができます。もしくは、サーマレスト社のスポーツシートをフォームシートとメッシュカバーの間に入れる事で高さ調整が出来るので、快適な高さになるまで空気調整をすると良いでしょう。この際注意してもらいたいことは、調整をすることでカヤックの安定性に大きな変化をもたらせないようにすることです。最後にもう一つ、ニンバスカヤックのシート調整システムで特有なことは、シートそのものをコックッピットの中で前後に動かせるということです。この調整をすることで、パドラーの体型を考慮した重量配置ができ、カヤックのバランスを取ることが可能になります。 |
 |
Each Nimbus(R) touring kayak is expedition outfitted with foot controlled, flip up rudder (some exceptions), large hatches and watertight compartments, bow chart holders, stern storage lines, foredeck storage tray, quick release paddle float attachment straps, a perimeter or tow line, and outside seams, all as standard equipment. |
 |
全てのニンバスのカヤックには、冒険に供えた装備を搭載しています。足でコントロールするフリップアップラダー(除外品あり)、大きなハッチと防水性の高い隔室、バウチャートホルダー、スターンのストレージライン、前デッキのストレージトレイ、パドルフロートをクイックリリースする為のストラップ、ペリメターまたは引き綱、外側のシーム。これらは全て標準装備です。
|
 |
(R) Kevlar is a registered trademark of E.I. du Pont de Nemours and Company. DuPont Canada Inc. is a licensee. |
ケブラーは、デュポン社の登録商標です。
|
|
ページトップへ▲ |
 |
お問い合わせはこちら |
 |